Transferring prints to a shirt is a creative and enjoyable way to personalize your clothing or even launch your own apparel brand. Whether you’re a DIY enthusiast or someone looking to explore the fashion or merchandising world, understanding how images and designs are transferred onto fabric is a valuable skill. With the right tools and materials, you can create professional-looking shirts from the comfort of your own home.
There are several popular methods of transferring prints to shirts, each with its own pros, cons, and ideal use cases. Choosing the right technique depends on your design, available equipment, and the number of shirts you plan to produce.
1. Heat Transfer Paper
One of the most accessible ways to print on shirts is through heat transfer paper. This method is especially suitable for beginners or those who only want to create a few custom pieces.
- What You Need: Inkjet printer, heat transfer paper, clothing iron or heat press, and a cotton or cotton-blend shirt.
- How It Works: You print your design onto special transfer paper using a regular inkjet printer. Once printed, you place the design face-down on the shirt and apply heat and pressure using an iron or a heat press to transfer the ink to the fabric.
Pros: Easy to use, affordable, and great for photo-quality designs.
Cons: Less durable over time and best suited for light-colored shirts.
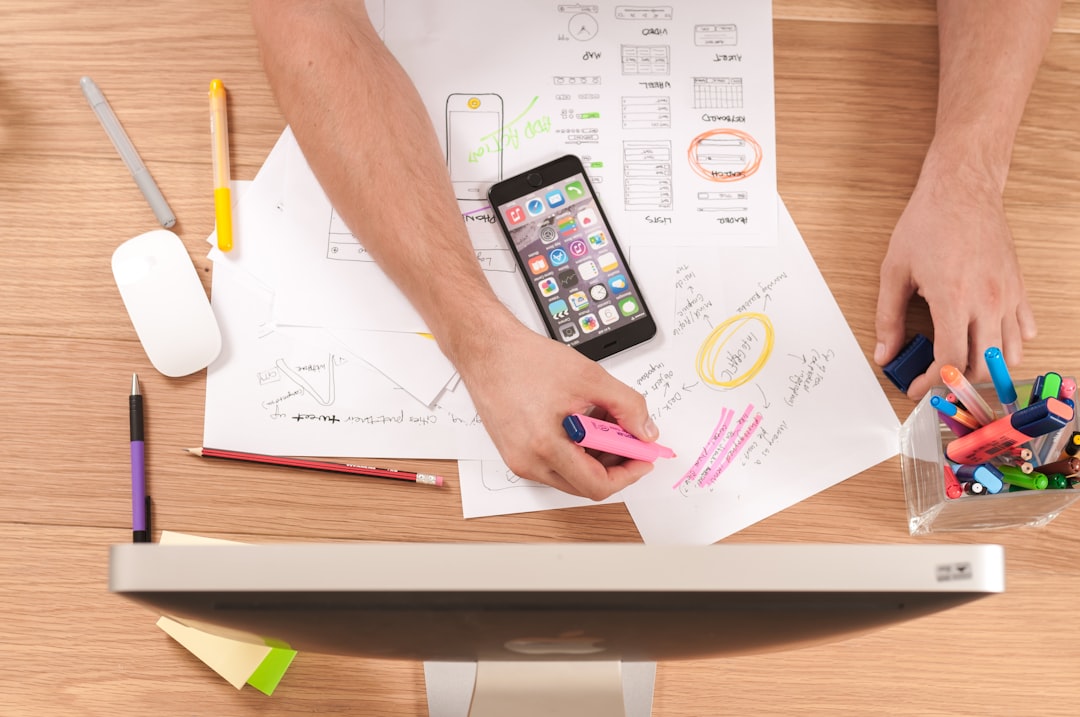
2. Sublimation Printing
Sublimation is a method that uses heat to transfer dye onto polyester fabrics. The unique feature of this technique is that it embeds the ink into the fabric, making the print incredibly durable and vibrant.
- What You Need: Sublimation printer, sublimation ink, sublimation paper, heat press, and polyester or high-poly blend shirts.
- How It Works: Your design is printed onto sublimation paper using special ink. When the paper is pressed onto the fabric with high heat, the ink turns into gas and bonds with the fabric fibers.
Pros: Long-lasting and vivid colors.
Cons: Only works on polyester fabrics and requires specialized equipment.
3. Screen Printing
Screen printing is a more hands-on, traditional technique that produces vibrant and long-lasting prints. It’s often used for bulk orders due to its efficiency and cost-effectiveness once the setup is complete.
- What You Need: Screen printing frame, emulsion, squeegee, fabric ink, and a light source.
- How It Works: A mesh screen is used to apply layers of ink through a stencil. Each color in the design will require a separate screen and printing pass.
Pros: Professional results, very durable, cost-effective for large quantities.
Cons: Time-consuming setup and not ideal for highly detailed, multi-colored images.
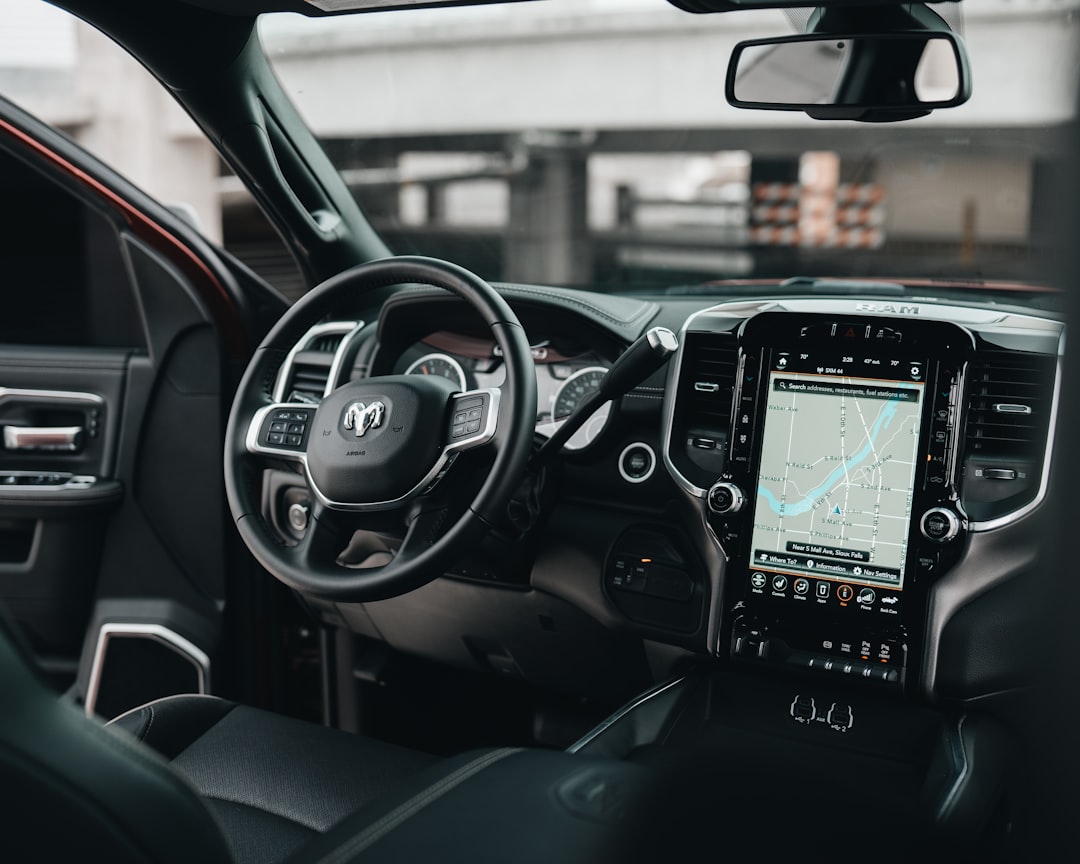
4. Direct-to-Garment (DTG) Printing
This method is like using an inkjet printer directly on fabric. Direct-to-garment printing excels in detail and color accuracy, making it a great choice for complex and full-color designs.
- What You Need: A DTG printer, fabric pretreatment solution, and cotton shirts.
- How It Works: The shirt is pretreated to ensure ink adhesion and then loaded into a DTG printer. The design is printed directly onto the fabric and then heat-set to secure the ink.
Pros: Excellent for detailed, full-color designs and small runs.
Cons: Equipment can be expensive and requires regular maintenance.
Tips for Best Results
- Use High-Quality Images: Always use high-resolution designs to avoid pixelation or blurry images.
- Prep Your Shirt: Make sure the shirt is clean and wrinkle-free before applying the design.
- Test First: If you’re trying a method for the first time, do a test run on an old shirt.
- Follow Instructions: Each material and printer type has unique heat and time settings—always read the guidelines carefully.
Conclusion
Transferring prints to shirts offers both artistic freedom and business opportunity. From using simple tools like a home inkjet printer to investing in professional-grade equipment, the possibilities are endless based on your needs and aspirations. Whether you want to create personalized gifts, start a clothing line, or decorate team apparel, all it takes is the right method and a bit of creativity. Start small, experiment, and enjoy the process of turning ideas into wearable art!